酸洗后奥氏体不锈钢锥形锻件局部出现数条沿圆周方向的裂纹。为找到开裂原因,研究了锻件制造过程,分析了不同位置的化学成分、拉伸性能、非金属夹杂物、显微组织、微观形貌及微区成分。结果表明:奥氏体不锈钢锥形锻件中存在含马氏体的异常组织,这些组织在酸洗过程中发生腐蚀,从而形成了沿圆周方向的条带状裂纹;建议加强冶炼过程中的质量管控及制造过程中的显微组织检验,防止马氏体出现,采取上述措施后再未出现过该类裂纹。
同一炉号026Cr19Ni10N控氮奥氏体不锈钢的锥形锻件在酸洗后,均出现数条沿圆周方向的裂纹,酸洗液均为5%(体积分数,下同)HF+15%HNO3 +80%H2O的混液,温度40~60℃ 。对裂纹处打磨后进行液体渗透检查时发现裂纹消失;对打磨表面再次进行酸洗后,裂纹又重新出现。锻件制造工艺主要包括钢锭冶炼、锻造、固溶热处理、粗加工(至筒形锻件)、理化性能分析、超声波检验、精加工(至锥形锻件)、酸洗和钝化等。钢锭炼过程包括 30t 电炉初炼 +30t 真空吹氧脱碳炉( VOD )精炼。电炉初炼时采用含氮奥氏体不锈钢的返回料,同时添加部分合金料(铬、镍、锰、硅等)和少量废钢,冶炼温度在1750~1800℃ ,保温4~5h ,以保证化学成分满足标准要求;在VOD精炼时,对钢液不断搅拌,并根据炉前分析结果补充精炼过程中可能会烧损的少合金元素,精炼温度控制在1800℃左右,保温2h 。精炼完成后,采用下浇注法(从钢模底部中心位置向上)一次浇注成5个钢锭,钢锭冒口端直径约850mm ,水口端直径约750mm ,长约1.3m 。
对钢锭头尾进行充分切除,冒口端切除量大于19% ,水口端切除量大于 6% ,以确保锻件无缩孔和严重偏析等缺陷,然后锻轧成直径约600mm的圆钢;在圆钢上钻孔并在具有足够压力的锻压机上扩孔至外径约1650mm 、内径约1020mm 、高约380mm的毛坯,温度控制在 850~1150℃ 。对锻造毛坯进行固溶处理:在250℃入炉,100℃.h-1速率升温至1060℃保温7.5h ,水冷。
将固溶处理的锻件毛坯粗加工至外径1635mm ,内径1035mm的筒形锻件,在距外表面20mm深的位置处取样并进行化学成分分析和室温拉伸试验;同时对锻件沿端面和圆周面进行超声波探伤。将筒形锻件机加工成厚度为24mm的锥形锻件,大端对应水口,小端对应冒口。对锥形锻件的所有表面进行液体渗透检测,检验合格后,用5%HF+15%HNO3 +80%H2O的混合溶液进行酸洗,温度40~60℃。酸洗后的锻件用清水清洗,再在温度为40~60℃ ,质量分数为20%的HNO3溶液中进行钝化处理。酸洗钝化时间根据锻件的表面状况以及溶液成分而确定。
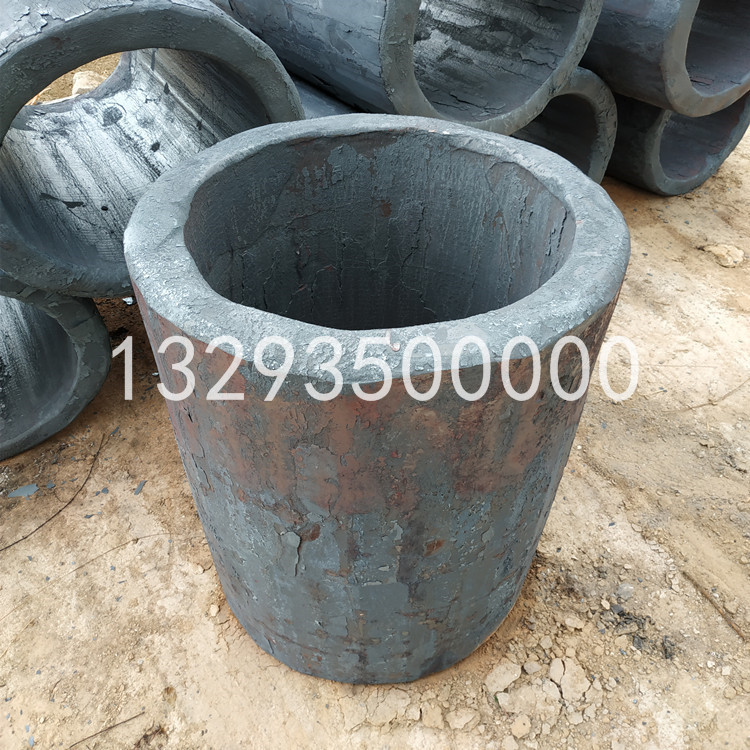
锻件开裂通常由下列原因造成:( 1 )夹杂物导致的开裂。在热变形加工过程中,当温度过低或锻造压力过大,锻件内部的夹杂物尺寸较大且不可变形时,夹杂物周边区域会产生应力集中,导致部分区域的应力超过材料本身强度,从而造成变形开裂。( 2 )加工应力过大导致的开裂。在热加工或机加工后,往往会在锻件表面形成残余拉应力,如果残余拉应力过大且在随后的。电池中的阳极,先被腐蚀溶解。此外,钝化膜的致密程度和铬富集程度有关,一般可用铬和铁含量的比值表示,该比值越高,说明钝化膜的保护性将越好。异常组织的铬含量较低,钝化膜的保护性较差,因此其耐腐蚀性较差。综上:由于该异常组织中的马氏体耐腐蚀性能较差,因此在酸洗过程中将先发生腐蚀,并在清洗后形成空洞;由于该空洞呈线性,因此在目视观察中将该类缺陷判断为裂纹。026Cr19Ni10N 控氮奥氏体不锈钢锻件经固溶处理后的正常组织为γ奥氏体,或者为 γ奥氏体+少量未溶δ铁素体。异常组织中马氏体的铬、镍含量相对于基体γ奥氏体的均偏低,这表明锻件制造厂所采购的铸锭存在局部化学成分异常。化学成分不均匀分布一般和钢锭的冶炼、浇铸及铸锭的凝固过程有关。在电炉冶炼时,炉料为该钢种的返炉料、合金料和少量废钢,通过在1750~1800℃保温足够时间以保证钢液充分熔化并使化学成分满足工艺要求。这个阶段的温度高、时间长,不会出现炉料的未熔化现象。在真空吹氧脱碳精炼时,通过底部吹氧气并不断搅拌来进行脱碳并使成分均匀化,同时根据炉前分析结果加入一定的烧损合金(如铬元素),如果加入的合金料未完全熔化,那么后期检测应该是合金元素(铬、镍)含量高于基体的。在精炼过程中并未出现合金料未熔化的情况。在浇铸过程中,采用下浇铸法,浇口位置位于铸锭钢模的下部中心位置,如果钢模中存在未清除干净的异物,如纯铁或低合金钢时,这些异物会被熔融钢液由下部冲刷至钢模上部,即接近钢锭冒口位置,并随后边熔化、边扩散,***终在靠近锻件小端位置形成沿圆周方向的点状或条状偏聚。这些偏聚区的铬、镍含量较低,在随后的固溶处理过程中转变成马氏体。
锻件不同位置的化学成分合格。但这些化学成分代表的是一定区域内的平均化学成分,反映不出不同相的成分差异,因此根据化学成分检测结果不能判断在靠近锥
形锻件小端位置处是否存在异常组织。